Graphite Electrode Uses For Corundum Refining Electric Arc Furnace Small Diameter Furnace Electrodes
Technical Parameter
Chart 1:Technical Parameter For Small Diameter Graphite Electrode
Diameter |
Part |
Resistance |
Flexural Strength |
Young Modulus |
Density |
C.T.E |
Ash |
|
Inch |
mm |
μΩ·m |
MPa |
GPa |
g/cm3 |
×10-6/℃ |
% |
|
3 |
75 |
Electrode |
7.5-8.5 |
≥9.0 |
≤9.3 |
1.55-1.64 |
≤2.4 |
≤0.3 |
Nipple |
5.8-6.5 |
≥16.0 |
≤13.0 |
≥1.74 |
≤2.0 |
≤0.3 |
||
4 |
100 |
Electrode |
7.5-8.5 |
≥9.0 |
≤9.3 |
1.55-1.64 |
≤2.4 |
≤0.3 |
Nipple |
5.8-6.5 |
≥16.0 |
≤13.0 |
≥1.74 |
≤2.0 |
≤0.3 |
||
6 |
150 |
Electrode |
7.5-8.5 |
≥8.5 |
≤9.3 |
1.55-1.63 |
≤2.4 |
≤0.3 |
Nipple |
5.8-6.5 |
≥16.0 |
≤13.0 |
≥1.74 |
≤2.0 |
≤0.3 |
||
8 |
200 |
Electrode |
7.5-8.5 |
≥8.5 |
≤9.3 |
1.55-1.63 |
≤2.4 |
≤0.3 |
Nipple |
5.8-6.5 |
≥16.0 |
≤13.0 |
≥1.74 |
≤2.0 |
≤0.3 |
||
9 |
225 |
Electrode |
7.5-8.5 |
≥8.5 |
≤9.3 |
1.55-1.63 |
≤2.4 |
≤0.3 |
Nipple |
5.8-6.5 |
≥16.0 |
≤13.0 |
≥1.74 |
≤2.0 |
≤0.3 |
||
10 |
250 |
Electrode |
7.5-8.5 |
≥8.5 |
≤9.3 |
1.55-1.63 |
≤2.4 |
≤0.3 |
Nipple |
5.8-6.5 |
≥16.0 |
≤13.0 |
≥1.74 |
≤2.0 |
≤0.3 |
Chart 2:Current Carrying Capacity For Small Diameter Graphite Electrode
Diameter |
Current Load |
Current Density |
Diameter |
Current Load |
Current Density |
||
Inch |
mm |
A |
A/m2 |
Inch |
mm |
A |
A/m2 |
3 |
75 |
1000-1400 |
22-31 |
6 |
150 |
3000-4500 |
16-25 |
4 |
100 |
1500-2400 |
19-30 |
8 |
200 |
5000-6900 |
15-21 |
5 |
130 |
2200-3400 |
17-26 |
10 |
250 |
7000-10000 |
14-20 |
Chart 3: Graphite Electrode Size & Tolerance For Small Diameter Graphite Electrode
Nominal Diameter |
Actual Diameter(mm) |
Nominal Length |
Tolerance |
|||
Inch |
mm |
Max. |
Min. |
mm |
Inch |
mm |
3 |
75 |
77 |
74 |
1000 |
40 |
-75~+50 |
4 |
100 |
102 |
99 |
1200 |
48 |
-75~+50 |
6 |
150 |
154 |
151 |
1600 |
60 |
±100 |
8 |
200 |
204 |
201 |
1600 |
60 |
±100 |
9 |
225 |
230 |
226 |
1600/1800 |
60/72 |
±100 |
10 |
250 |
256 |
252 |
1600/1800 |
60/72 |
±100 |
Main Application
- Calcium carbide smelting
- Carborundum production
- Corundum refining
- Rare metals smelting
- Ferrosilicon plant refractory
RP Graphite Electrode Production Process
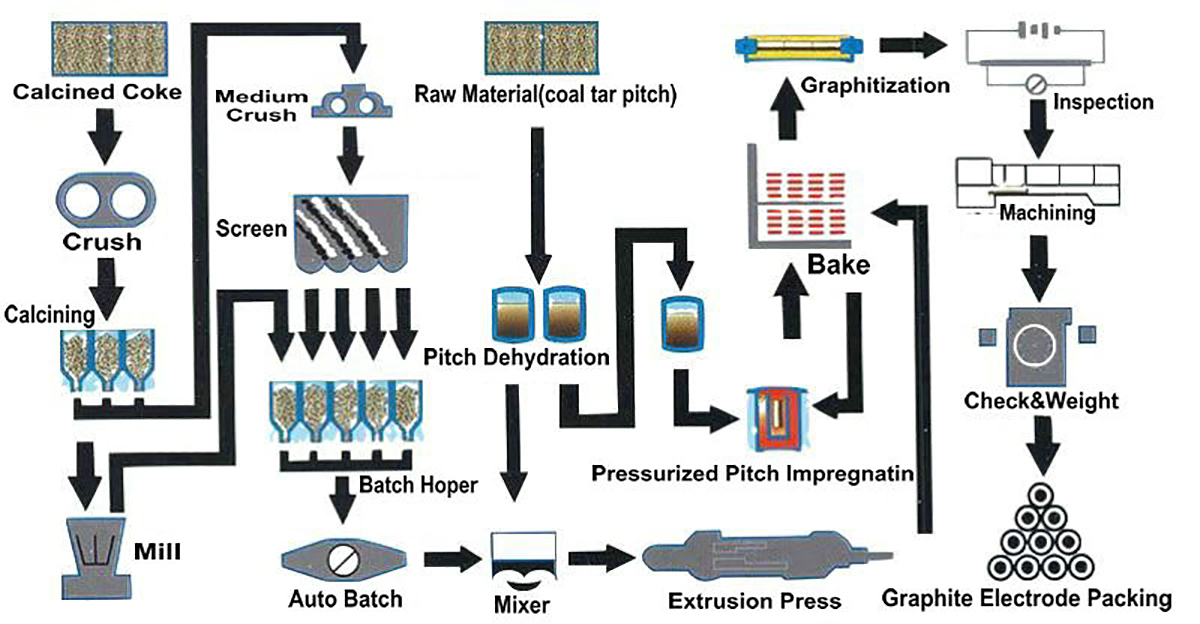
Gufan Advantages
1. Made from high-quality graphite materials, our small diameter graphite electrodes are built to withstand extreme temperatures and provide excellent electrical conductivity. This ensures a stable and efficient smelting process, resulting in superior product quality and reduced energy consumption.
2. The small size of these electrodes allows for more precise control over the smelting process, making them perfect for applications that require high accuracy and fine-tuned results. Whether you are producing alloys or refining metals, our electrodes will help you achieve the desired outcome with unmatched precision.
3. Our small diameter graphite electrodes are suitable for a wide range of industries, including steel manufacturing, chemical processing, and metal casting. No matter the size of your operation, our electrodes can be customized to meet your specific requirements.
4. In steel manufacturing, our small diameter graphite electrodes are utilized in electric arc furnaces, where they play a crucial role in the production of high-quality steel. Their small size allows for precise control over the melting process, ensuring consistent results and minimizing waste.
5. In chemical processing, our electrodes are essential for the production of calcium carbide and the refinement of carborundum. These processes require precise temperature control, which our electrodes deliver with utmost accuracy.
6. For metal casting, our small diameter graphite electrodes are used in the smelting of rare metals and Ferrosilicon plants. The superior conductivity of graphite allows for efficient melting of metals, resulting in faster production cycles and higher overall productivity.