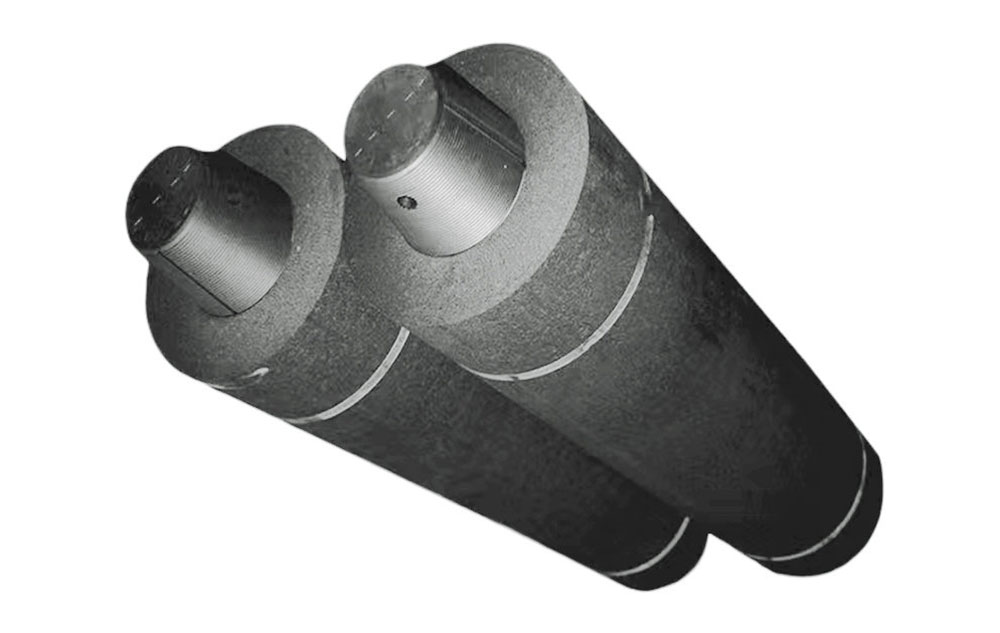
Because of graphite electrodes’ excellent performance including high conductivity, high resistance to thermal shock and chemical corrosion and low impurity, graphite electrodes are playing a crucial role in EAF steelmaking during modern steel industry and metallurgy for demanding of improve efficiency, reduce costs, and promote sustainability.
What Is Graphite Electrode?
GRAPHITE ELECTRODES are the best conductive material for electric arc furnace and smelting furnace,They produced by the high quality needle cokes mixed,molded,baked and graphitization process to form the finished product.GRAPHITE ELECTRODES are well suited for use in high-temperature environments and can withstand extreme heat without breaking down.It is presently the only available product that has the high levels of electrical conductivity and the capability of sustaining the extremely high levels of heat generated in the demanding environment.
This feature reduces the energy losses and improves the entire smelting process' efficiency, resulting in less energy consumption and lower production costs.
Graphite Electrode Unique Properties
GRAPHITE ELECTRODE is ideal for using in electric arc furnaces and other industrial applications.The unique properties ensure graphite electrode can withstand high temperatures reaching up 3,000°C to and pressures in electric arc furnace(EAF).
- High Thermal Conductivity- Graphite electrodes have excellent thermal conductivity, which enables them to withstand high temperatures and pressures during the melting process.
- Low Electrical Resistance- The low electrical resistance of graphite electrodes facilitates the easy flow of electrical energy in electric arc furnaces.
- High Mechanical Strength- Graphite electrodes are designed to have high mechanical strength to withstand the high temperature and pressure levels in electric arc furnaces.
- Excellent Chemical Resistance- Graphite is a highly inert material that is resistant to most chemicals and corrosive substances. Graphite electrodes ideal for use in harsh industrial environments, where other materials may fail due to chemical attack.
Graphite electrodes are not only widely used in electric arc furnaces,also used in the production of silicon metal, yellow phosphorus, and other non-ferrous metals,acids, alkalis, and other chemicals, corrosive environments.
Graphite electrodes are classified into three grades based on their physical properties ,specifications and different applications related the electric furnace capacity, transformer power load. The most commonly used grades of graphite electrodes are Ultra-high power (UHP), High power (HP), and Regular power (RP).
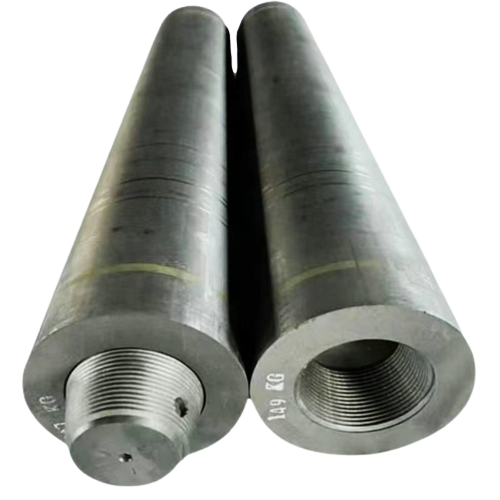
UHP graphite electrodes feature high thermal conductivity and low electrical resistance,they are specially used for ultra-high power electric arc furnace(EAF) in smelting of refined steel or special steel.UHP graphite electrode is suitable the electric furnace capacity is 500~1200kV/A per ton.
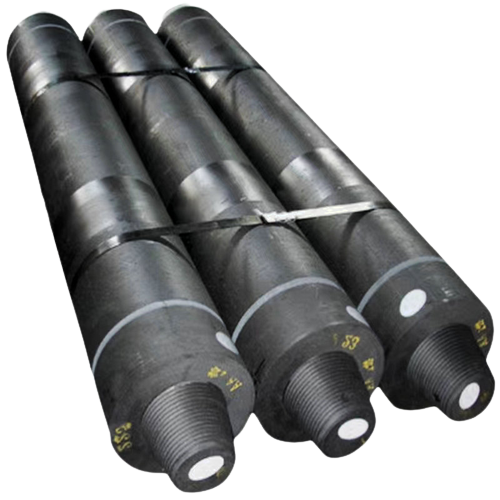
HP Graphite Electrode is the best conductive material for electric arc furnace and smelting furnace,it acts as a carrier to introduce current into the furnace.HP graphite electrode is normally used for higher power electric arc furnace(EAF) which capacity is around 400kV/A per ton.
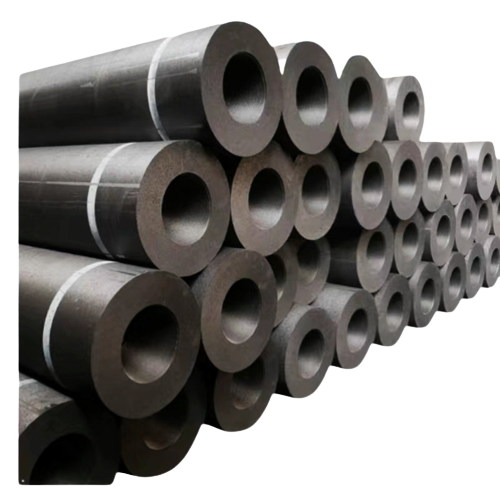
RP graphite electrode is widely used in regular power electric furnace which capacity is around 300kV/A per ton or less.The RP grade has the lowest thermal conductivity and mechanical strength compared to UHP graphite electrode and HP graphite electrode.RP graphite electrodes are more suitable for the production of lower-grade metals such as steelmaking, refining silicon, refining yellow phosphorus, producing glass industries.
With the growing demand for alternative power sources, graphite electrodes are also playing an important role in the development of fuel cells.
Graphite electrodes have a wide range of applications in various industries. Some of the primary applications of graphite electrode include;
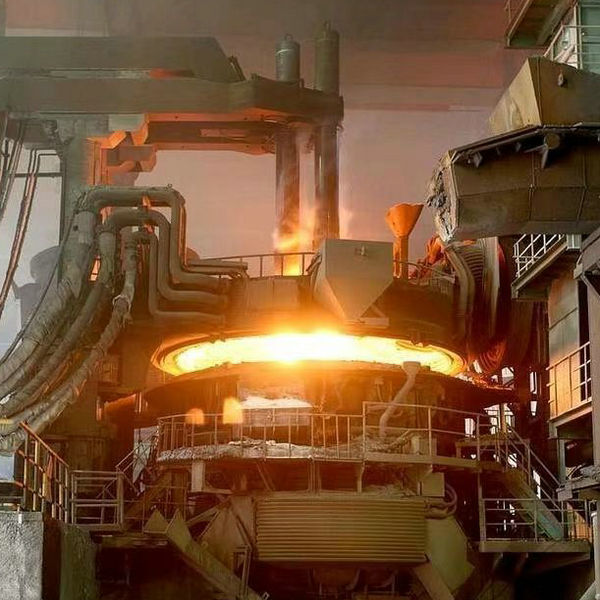
Electric Arc Furnace(EAF) in Steelmaking
Graphite electrode application in EAF steelmaking is a key aspect of modern steel production. Graphite electrodes are as a conductor to deliver electricity to the furnace, which in turn produces heat to melt the steel.The EAF process requires high temperatures to melt the scrap steel, graphite electrodes can withstand high temperatures without losing their structural integrity.As the world continues to focus on sustainable and efficient production methods, graphite electrodes will continue to play a crucial role in EAF steelmaking.
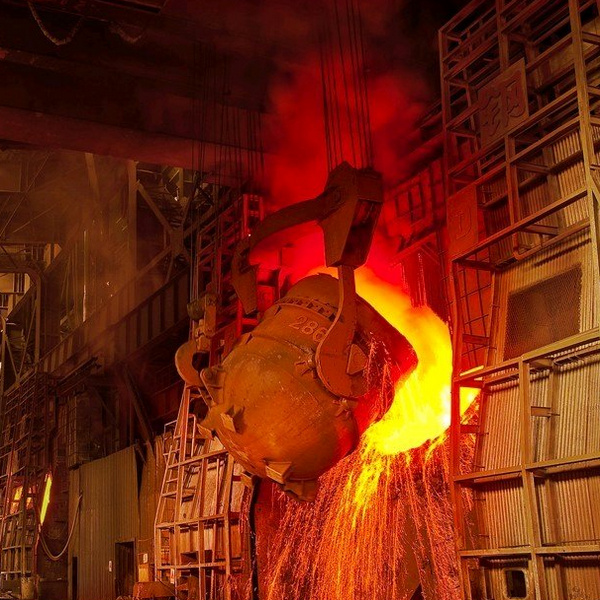
Ladle Furnace(LF)
Ladle furnaces(LFs) are vital components of the steel-making Process.Graphite electrodes are used in the ladle furnace industry to provide the highest electrical current and high temperature throughout the process. The graphite electrodes own the excellent features including high conductivity, resistance to thermal shock and chemical corrosion, and long lifespan, they are the ideal choice for ladle furnace(LF) application.By using graphite electrodes, ladle furnace operators can achieve greater efficiency, productivity and cost-effectiveness, while maintaining the high quality standards that the industry demands.
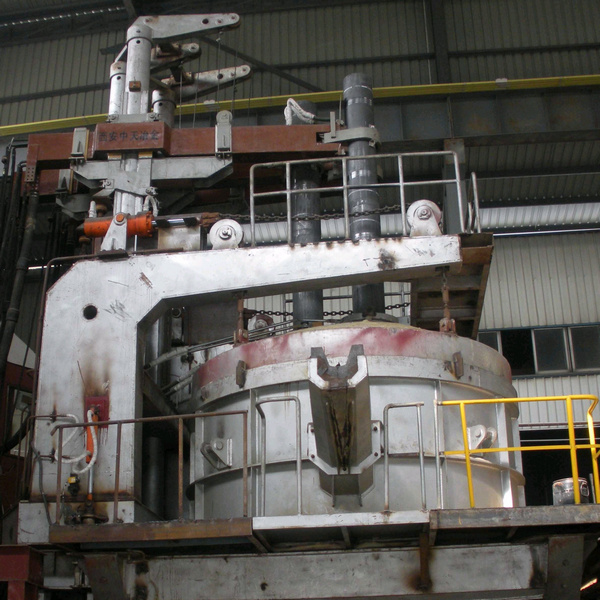
Submerged Electric Furnace(SEF)
Graphite electrodes are widely used in submerged electric furnace is a crucial element in the production of many metals and materials such as yellow phosphorus, pure silicon. Graphite electrodes own the excellent feature including high electrical conductivity, high resistance to thermal shock, and low coefficient of thermal expansion. These features make graphite electrode ideal for use in submerged electric furnaces, where extreme temperatures and harsh conditions are the norm.
Graphite electrodes are crucial components in the Electric Arc Furnace (EAF) steelmaking process.The graphite electrode consumption a critical cost element in steel production.How to select the proper grade and size for graphite electrode,there are several factors to consider for any application.
- Steel type and grade
- Burner and oxygen practice
- Power level
- Current level
- Furnace design and capacity
- Charge material
- Target graphite electrode consumption
Selecting the proper graphite electrode for your furnace is critical to achieving optimal performance, minimizing energy consumption, and reducing maintenance costs.
Chart For Recommend Matching For Electric Furnace With Electrode
Furnace Capacity (t) |
Inner Diameter (m) |
Transformer Capacity (MVA) |
Graphite Electrode Diameter (mm) |
||
UHP |
HP |
RP |
|||
10 |
3.35 |
10 |
7.5 |
5 |
300/350 |
15 |
3.65 |
12 |
10 |
6 |
350 |
20 |
3.95 |
15 |
12 |
7.5 |
350/400 |
25 |
4.3 |
18 |
15 |
10 |
400 |
30 |
4.6 |
22 |
18 |
12 |
400/450 |
40 |
4.9 |
27 |
22 |
15 |
450 |
50 |
5.2 |
30 |
25 |
18 |
450 |
60 |
5.5 |
35 |
27 |
20 |
500 |
70 |
6.8 |
40 |
30 |
22 |
500 |
80 |
6.1 |
45 |
35 |
25 |
500 |
100 |
6.4 |
50 |
40 |
27 |
500 |
120 |
6.7 |
60 |
45 |
30 |
600 |
150 |
7 |
70 |
50 |
35 |
600 |
170 |
7.3 |
80 |
60 |
--- |
600/700 |
200 |
7.6 |
100 |
70 |
--- |
700 |
250 |
8.2 |
120 |
--- |
--- |
700 |
300 |
8.8 |
150 |
--- |
--- |
700 |